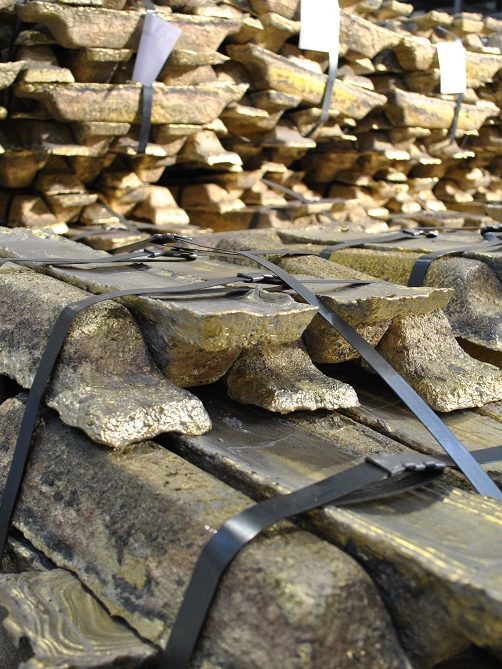
AGIPRES manufactures BRASS and BRONZE ALLOY DIE-CASTING PRODUCTS, with DIFFERENT WEIGHTS, which vary between 5 grams and 7 kilograms.
AREAS OF APPLICABILITY
To work in the field of die-casting means, on one hand to combine rough materials and design and on the other to aim for refined and meticulous finishings. The die-casting sector requires a high level of respect towards aesthetics and design.
In order to obtain the best aesthetic result out of fusion and finishings (tumbling and abrasive blasting), AGIPRES puts a great deal of effort into the designing and the feasibility studying of the die-casting process.
PROCESS
The cast metal is injected high pressure into a metal mold without a pattern: the metal is cast in a form consisting of two semi-pressurized metal molds.
To ensure the cooling of the piece, there is a fluid circulation system inside the mold. Once the piece is solidified and cooled, the presses open the two molds so that it can be picked up.
Die-casting can be divided into:
• Hot chamber pressed = the molten metal tank is inserted into a furnace.
• Cold chamber die casting = Metal reservoir is a simple cavity not controlled temperature.